煤与矸石机器人自动分拣系统
一、项目背景
1、多年来在煤矿提升系统始终有一只敢于打硬仗的队伍:拣矸队。该队伍承担的任务就是煤矸分离:自主井提升上来的原煤,经过初次筛分后,通过人工手动分选原煤、矸石。环境恶劣,分拣效率低下,对操作人员造成重大身心伤害。
2、国家安全生产监督管理总局 安监总科技〔2015〕63号
关于开展“机械化换人、自动化减人”科技强安专项行动的通知 内容重点:是以机械化生产替换人工作业、以自动化控制减少人为操作,大力提高企业安全生产科技保障能力。
3、《煤矿安全生产“十三五”规划》主要任务:(三)推进煤矿安全基础建设,推进煤矿机械化 自动化、信息化、智能化改造。
4、2016版本《煤矿安全规程》第657条 作业人员每天连续接触噪声时间达到或者超过8小时的,噪声声级限值为85dB。
第659条 应当优先选用低噪声设备,采取隔声、消声、吸声、减振、减少接触时间等措施降低噪声危害。
5、2016版本《煤矿安全规程》第640条 作业场所空气中粉尘浓度应当符合要求。不符合要求的,应当采取有效措施。
二、项目重大意义
1、填补国际、国内技术空白,技术原创,达到国际领先水平。
2、切身保护员工身心健康,远离高浓度粉尘、噪音大空间。
3、摈弃人工拣矸,提高拣矸效率、准确率。
4、机械化换人、自动化减人,减员增效。
5、打破行业内顽疾,促进煤炭工业科技进步。
三、项目核心技术
1、图像识别处理技术(基于大数据算法)
2、机器人智能分拣技术
四、煤矸手选现场问题
1、手选皮带现场是利用人工进行手动拣煤,矸石直接通过皮带两侧漏斗分流至缓冲仓内,由缓冲仓向轨道上矿车进行矸石装载,运输至矸石山。块煤由人工挑选放在皮带上继续前行,经破碎到达主运皮带汇入选煤厂。各个煤矿现场工艺路线各有不同,但最终都是通过人工手选进行煤矸分离。
2、经过现场调研分析,基于人的视觉及手部频繁重复运动的疲劳状况,这种人工手动筛分效果较差,误拣率高,块煤分拣成功率最多达到80%,造成一定程度的浪费,降低生产效率。
3、根据我们公司技术人员现场实际调研,在主井口原煤振动筛处进行噪声分贝测试,在距离振动筛1m处噪声声级普遍达到120dB,属于严重超标,违反了《煤矿安全规程》的相关规定。
4、主井口原煤振动筛在振动的过程中产生大量的粉尘,严重超标,主要是因为振动的原理,对筛面进行密封难度太大。
5、根据现场实际情况观察,手选皮带走廊内拥有大量的粉尘,以及严重超标的噪音,严重伤害现场操作工的身心健康。
五、项目实施方案
1、通过对煤与矸石数字图像频谱分析,基于深度学习特征提取,利用大数据进行综合计算分析,最终由软件对煤与矸石进行了完全准确识别。
2、在软件识别煤与矸石的同时,发出信号给与机器人,由机器人在特定区域执行智能分选的操作,将煤与矸石依据现场工艺路线进行分离,实现智能分拣,摈弃人工手选矸石的操作。
3、将现场的振动筛更换为滚动筛,实现不振动筛分,在筛分的过程中进行筛片清扫处理,确保筛透率,提高筛分效率,确保小颗粒被筛分掉,不在进入二次筛选。
4、将现场振动筛更换为矿用滚动筛,在距离滚动筛1m处噪声声级普遍为75dB,中矿恒扬设计的矿用滚动筛是在完全密封的状态下工作,不产生任何粉尘,完全符合《煤矿安全规程》规定。
六、改造效果总结
1、面对手选矸石现场存在的各种问题,通过对国内外最先进技术的应用,进行逐条解决,做到完全符合2016年新版《煤矿安全规程》关于噪音、粉尘等相关规定,符合环保要求,将分选系统建设成为标准化矿井、本质安全型矿井,在整个煤炭行业内率先树立起标杆。
2、通过新产品、新技术的应用,减员增效,实现煤与矸石智能化分选,达到“无人值守”状态,系统自动化程度极高,充分实现国家煤监局要求的“机械化换人,自动化减人”的目标;大幅提高企业的安全生产水平;大力推进煤矿机械化、自动化、信息化和智能化的“四化”建设。
3、该项目建设具有极高的行业推广价值,目前在国内外煤矿行业内,人工拣矸现象非常普遍,范围之广,上至央企诸如中煤集团、神华集团等,下至地方小型煤矿,全国一盘棋,均是采用人海战术,在上井口手选皮带动态工作的情况下,需要拣矸工人眼疾手快,时刻保持精力充沛,不能有任何分心,而且必须保持站姿,劳动强度之大,环境之恶劣,实属常人难以承受。煤与矸石智能分离系统具有极高的推广价值,为煤矿的筛分技术做出了极大的贡献。
4、切身保护现场操作工身心健康,远离高浓度粉尘、高噪音的生产空间。
5、摈弃人工拣矸,增强拣煤准确率,提高煤矿生产效率。
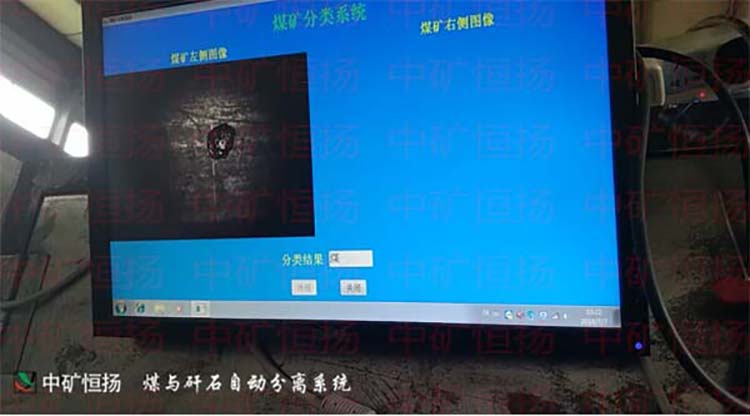
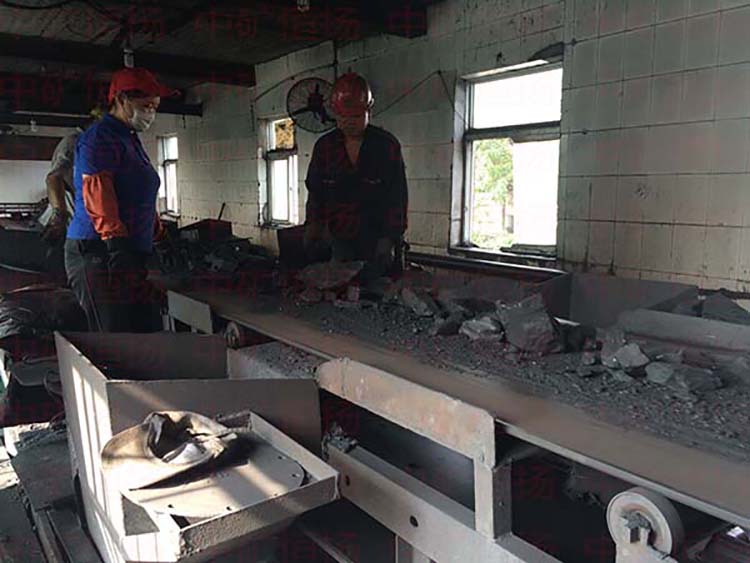
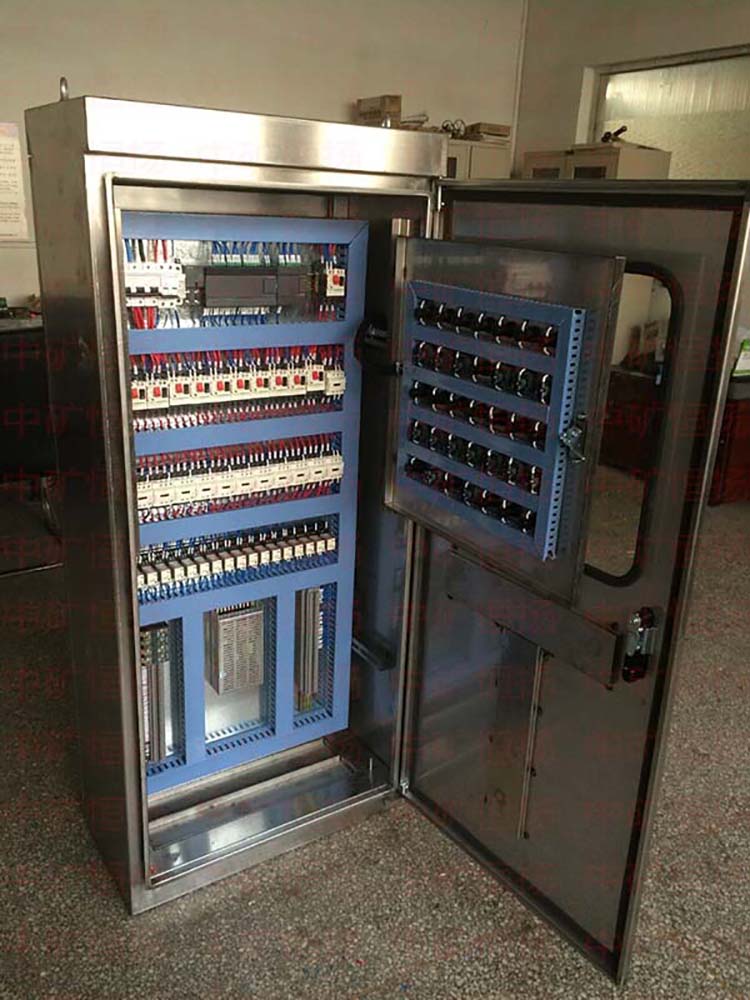
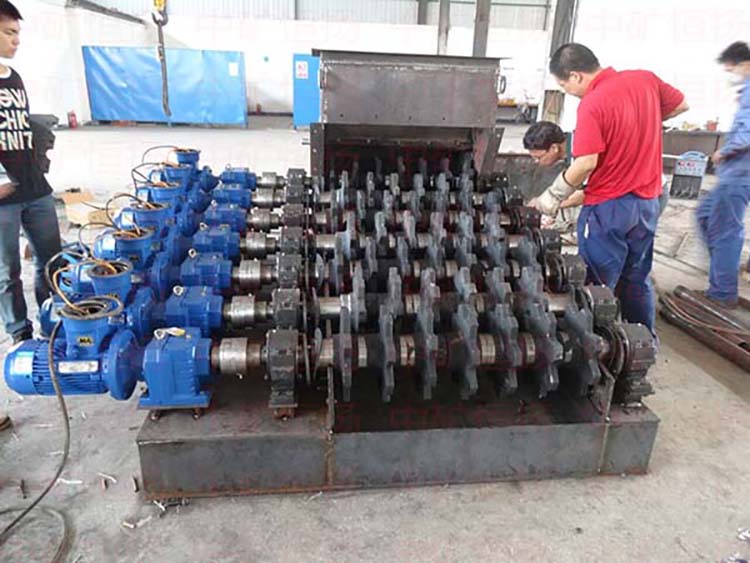
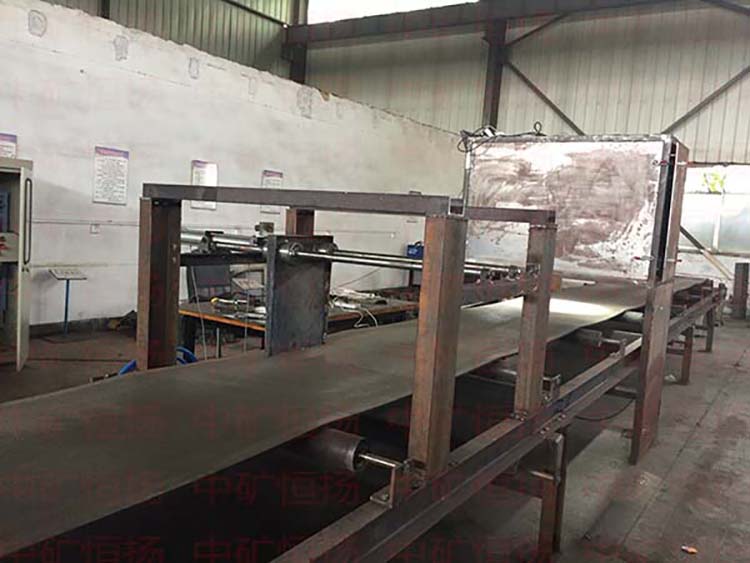